鋼結構檢測
西安建大維固工程檢測鑒定有限公司
24小時免費熱線
劉工:182-9296-7937(全國免費熱線)
李工:180-6652-0076(微信同號)
公司地址:
西安市雁塔路13號
公司網址:www.lcixpe.cn
我公司多年從事鋼結構檢測、金相檢測、力學檢測等業務,經驗豐富,是寶鋼指定服務商,曾經參與過國家鳥巢體育館、南京火車站、恒隆廣場、越南電廠等諸多大型項目,實力雄厚,技術先進,是您可靠的檢測合作伙伴,為您竭誠服務。
一.無損檢測
無損檢測簡稱NDT (Non-destructive testing)是工業發展必不可少的有效工具,在一定程度上反映了一個國家的工業發展水平,其重要性已得到公認。無損檢測NDT (Non-destructive testing),就是利用聲、光、磁和電等特性,在不損害或不影響被檢對象使用性能的前提下,檢測被檢對象中是否存在缺陷或不均勻性,給出缺陷的大小、位置、性質和數量等信息,進而判定被檢對象所處技術狀態(如合格與否、剩余壽命等)的所有技術手段的總稱。
無損檢測的方法有:
超聲檢測 Ultrasonic Testing(縮寫 UT);
射線檢測 Radiographic Testing(縮寫 RT);
磁粉檢測 Magnetic particle Testing(縮寫 MT);
滲透檢驗 Penetrant Testing (縮寫 PT);
射線和超聲檢測主要用于內部缺陷的檢測;磁粉檢測主要用于鐵磁體材料制件的表面和近表面缺陷的檢測;滲透檢測主要用于非多孔性金屬材料和非金屬材料制件的表面開口缺陷的檢測;鐵磁性材料表面檢測時,宜采用磁粉檢測。渦流檢測主要用于導電金屬材料制件表面和近表面缺陷的檢測。
當采用兩種或兩種以上的檢測方法對構件的 同一部位進行檢測時,應按各自的方法評定級別;采用同種檢測方法按不同檢測檢測工藝進行檢測時,如檢測結果不一致,應危險大的評定級別為準。
(1) 射線檢測
(1) 射線檢測
射線檢測就是利用射線(X射線、γ射線、中子射線等)穿過材料或工件時的強度衰減,檢測其內部結構不連續性的技術。穿過材料或工件時的射線由于強度不同,在感光膠片上的感光程度也不同,由此生成內部不連續的圖像。
射線檢測主要應用于金屬、非金屬及其工件的內部缺陷的檢測,檢測結果準確度高、可靠性好。膠片可長期保存,可追溯性好,易于判定缺陷的性質及所處的平面位置。
射線檢測也有其不足之處,難于判定缺陷在材料、工件內部的埋藏深度;對于垂直于材料、工件表面的線性缺陷(如:垂直裂紋、穿透性氣孔等)易漏判或誤判;同時射線檢測需嚴密保護措施,以防射線對人體造成傷害;檢測設備復雜,成本高。
射線檢測只適用于材料、工件的平面檢測,對于異型件及T型焊縫、角焊縫等檢測就無能為力了。
(2) 超聲波檢測
超聲波檢測就是利用超聲波在金屬、非金屬材料及其工件中傳播時,材料(工件)的聲學特性和內部組織的變化對超聲波的傳播產生一定的影響,通過對超聲波受影響程度和狀況的探測了解材料(工件)性能和結構變化的技術。
超聲波檢測和射線檢測一樣,主要用于檢測材料(工件)的內部缺陷。檢測靈敏度高、操作方便、檢測速度快、成本低且對人體無傷害,但超聲波檢測無法判定缺陷的性質;檢測結果無原始記錄,可追溯性差。
超聲波檢測同樣也具有著射線檢測無法比擬的優勢,它可對異型構件、角焊縫、T型焊縫等復雜構件的檢測;同時,也可檢測出缺陷在材料(工件)中的埋藏深度。
(3) 磁粉檢測
磁粉檢測是利用漏磁和合適的檢測介質發現材料(工件)表面和近表面的不連續性的。
磁粉檢測作為表面檢測具有操作靈活、成本低的特點,但磁粉檢測只能應用于鐵磁性材料、工件(碳鋼、普通合金鋼等)的表面或近表面缺陷的檢測,對于非磁性材料、工件(如:不銹鋼、銅等)的缺陷就無法檢測。
磁粉檢測和超聲波檢測一樣,檢測結果無原始記錄,可追溯性差,無法檢測到材料、工件深度缺陷,但不受材料、工件形狀的限制。
(4) 滲透檢驗
滲透檢驗就是利用液體的毛細管作用,將滲透液滲入固體材料、工件表面開口缺陷處,再通過顯像劑滲入的滲透液吸出到表面顯示缺陷的存在的檢測方法。
滲透檢驗操作簡單、成本很低,檢驗過程耗時較長,只能檢測到材料、工件的穿透性、表面開口缺陷,對僅存于內部的缺陷就無法檢測。
(5) 射線檢測、超聲波檢測
射線檢測、超聲波檢測是對材料、工件內部缺陷檢測的主要手段,廣泛應用于鋼結構、鍋爐、壓力容器、鑄造等行業。通過缺陷的性質、大小來判斷缺陷的危害程度,同時判定缺陷的位置,以利于準確的修復。
磁粉檢測、滲透檢測作為表面缺陷和穿透性缺陷的檢測,是對射線檢測、超聲波檢測的有力補充。
TOFD 原理是當超聲波遇到諸如裂紋等的缺陷時,將在缺陷尖端發生疊加到正常反射波上的 衍射波,探頭探測到衍射波,可以判定缺陷的大小和深度。當超聲波在存在缺陷的線性不連續處,如裂紋等處出現傳播障礙時,在裂紋端點處除了正常反射 波以外,還要發生衍射現象。衍射能量在很大的角度范圍內放射出并且假定此能量起源于裂紋末端。這與依賴于間斷反射能量總和的常規超聲波形成一個顯著的對比。
根據TOFD的理論和特點,在檢測后壁容器方面具有巨大的優勢,在國內使用的初期階段要充分發揮其有點,使用其他技術彌補其缺點,讓TOFD技術更快的應用到檢測中。(超聲波檢測的一種,目前無損檢測研究部新發展的檢測方向)
1.不損壞試件材質、結構
1.不損壞試件材質、結構
無損檢測的最大特點就是能在不損壞試件材質、結構的前提下進行檢測,所以實施無損檢測后,產品的檢查率可以達到100%。但是,并不是所有需要測試的項目和指標都能進行無損檢測,無損檢測技術也有自身的局限性。某些試驗只能采用破壞性試驗,因此,在目前無損檢測還不能代替破壞性檢測。也就是說,對一個工件、材料、機器設備的評價,必須把無損檢測的結果與破壞性試驗的結果互相對比和配合,才能作出準確的評定。
2.正確選用最適當的無損檢測方法
由于各種檢測方法都具有一定的特點,為提高檢測結果可靠性,應根據設備材質、制造方法、工作介質、使用條件和失效模式,預計可能產生的缺陷種類、形狀、部位和取向,選擇合適的無損檢測方法。
3.綜合應用各種無損檢測方法
任何一種無損檢測方法都不是萬能的,每種方法都有自己的優點和缺點。應盡可能多用幾種檢測方法,互相取長補短,以保障承壓設備安全運行。此外在無損檢測的應用中,還應充分認識到,檢測的目的不是片面追求過高要求的“高質量”,而是應在充分保證安全性和合適風險率的前提下,著重考慮其經濟性。只有這樣,無損檢測在承壓設備的應用才能達到預期目的。
4.鈞測鋼結構檢測實驗室簡介
工程技術公司的鋼結構檢測專業隸屬鈞測建設,除“國家實驗室認可(國家技術監督局認可委頒證)”、“寶鋼工程質量監督站檢測中心(原冶金部質量監督總站頒證)”共享資質、“上海市建設工程鋼結構質量檢測單位”和“上海寶鋼冶金建設公司壓力管道安裝無損檢測(GA、GB、GC)”等資質和資格,,還單獨具有“鍋爐壓力容器、壓力管道、特種設備無損檢測單位資格(國家質量監督檢驗檢疫總局頒證)”、“無損檢測專業承包壹級(建設部頒證)”并取得上海市環保局頒發的“輻射安全許可證證” ,出具的檢測報告數據科學、公正、準確,并可得到國際互認。
鋼結構檢測業務范圍包括鋼結構和特種設備的原材料、焊材、焊接件、緊固件、焊縫、螺栓球節點、涂料等材料和工程的全部規定的試驗檢測內容。
在提升單項檢測技術的同時,注重發展和實現專業間的一體化,完善了成套的鋼結構檢測技術,包括鋼結構力學性能檢測(拉伸、彎曲、沖擊、硬度)、鋼結構緊固件力學性能檢測(抗滑移系數、軸力)、鋼結構金相檢測分析(顯微組織分析、顯微硬度測試)、鋼結構化學成分分析、鋼結構無損檢測、鋼結構應力測試和監控、涂料檢測等成套檢測技術。
目前,配備的鋼結構檢測先進設備一應俱全,其中厚板檢測用200t萬能材料試驗機,質量仲裁用的30t伺服式萬能材料試驗機,低溫沖擊試驗機(-180℃)、數控式緊固件測試設備、美國進口的AA800原子吸收分析儀、俄羅斯引進的Se75γ射線探傷儀等設備均達到了上海市一流乃至國內領先水平。T、K、Y相貫焊縫節點超聲波探傷技術、同位素Se75γ射線探傷在特種設備中的應用等特殊結構無損檢測技術曾分別榮獲上海市優秀發明選撥賽一、二等獎。
鋼結構檢測緊跟國際鋼結構檢測技術發展潮流,培養出一批高素質的鋼結構檢測專業技術人員,現擁有無損檢測高級(Ⅲ)人員5名,中級(Ⅱ)人員28名,高級工程師12名,工程師16名,技師3名。
多年來,鋼結構及特種承壓設備檢測專業隊伍在冶金市場上,足跡遍布全國各大鋼廠,特別是在寶鋼一、二、三期,十五規劃工程鋼結構檢測中積累了豐富的經驗,除了以上還負責寶鋼內全部壓力容器、壓力管道的在役檢測,為了面向社會向更廣闊的市場業務范圍發展,我們足跡遍布全國,先后承接了上海磁懸浮列車、盧浦大橋、北京奧運工程——國家體育場(鳥巢)、央視大樓等重大工程鋼結構檢測以及天然氣西氣東輸工程安徽蕪湖三個標段的壓力管道檢測、寶鋼化工壓力容器、管道、反應塔等裝置檢測,另外我們還承接了上海高橋石化煉油裝置的檢測、上海焦化廠一氧化碳、乙烯等裝置的管道檢測,還承擔了美國舊金山大橋輔橋鋼結構工程等工程檢測業務。
我們有各種磁粉檢測儀11臺;超聲波(進口、國產)共10臺;X射線機5臺;γ射線機7臺,工程檢測車3臺,還配備有各種輔助檢測器具(射線機爬行器等)。
二.金相檢測
金相即金相學,就是研究金屬或合金內部結構的科學。不僅如此,它還研究當外界條件或內在因素改變時,對金屬或合金內部結構的影響。
金相檢測研究室創建于上世紀90年代初,經過十多年的逐步發展和不斷完善,先后通過國家認可委員會實驗室認可、冶金工業工程質量監督總站檢測中心認可、三合一管理體 系認證,并且參與了上海市工程建設規范《鋼結構檢測與鑒定技術規程 DG/TJ08-2011-2007》的編寫工作,現為專業的金相檢驗第三方實驗室。目前,金相檢測研究室配備了在國內外均屬一流的金相制樣與檢測設備,再輔以金相圖像分析系統,真正實現檢測工作一體化。
金相檢測研究室長期從事寶鋼廠區鋼(鐵)水包檢驗、混鐵車、行車檢驗以及各種壓力容器管道以及特種設備檢驗,另外還囊括周邊地區各大冶建單位的工藝評定業務。近年來,作為專業的第三方檢測機構,已為各大生產廠家進行產品質量的出廠檢驗。同時,在長三角地區承接了許多采用歐標、美標等國外企業的檢測業務,并且在化工、鋼鐵、石油、民房等各行業均有檢測業務的介入,使金相檢測向更寬更廣的領域發展。
一、檢測流程
客戶送樣至我公司-填寫委托-收樣人確認-客戶所取委托號和報告取用單-我公司在3~5個工作日(或與客戶約定日期)完成檢測任務-出具報告-客戶評報告取用單附費取報告。具體按公司檢測站流轉。
二、技術規范
1、TB 10212-2008《鐵路鋼橋制造規范》
2、DG/TJ08-2001-2007(J10973-2007)《鋼結構檢測與鑒定技術規程》
3、DG/TJ08-804-2005(J10616-2005)《既有建筑物結構檢測與評定標準》
4、GB/T 17455-1998《無算檢測 表面檢查的金相復制件技術》
5、DNV 船舶入級規范《船舶/高速、輕型船只和海軍水面船只-新建船只》
6、BS EN 1321-1996《Destructive tests on welds in metallic materials-Macroscopic and microscopic examination of welds》
7、E45-05 《Standard Test Methodds for Determining the inclusion Content of Steel》
8、GB/T 3949-2001《船用不銹鋼焊接接頭晶間腐蝕試驗方法》
9、ISO 9015-1:2001《金屬材料焊縫破壞性試驗-硬度試驗-第一部分:弧焊接頭的硬度試驗》。
10、ISO 9015-2:2001《金屬材料焊縫破壞性試驗-硬度試驗-第二部分:弧焊接頭的硬度試驗》
11、BS EN 287-1:2004《Qualification test of welders-Fusion welding-Part 1:Steel》
12、GB/T 5617-2005《鋼的感應淬火或火焰淬火后有效硬化層深度的測定》
13、DL/T 868-2004《焊接用以評定規程》
14、DL/T 773-2001《火電廠用12CrMoV鋼球化評級標準》
15、EN 1320《Destructive tests on welds in metallic materials-Fracture test》
16、GB.T6417.1-2005/ISO 6520-1:1998《金屬熔化焊接頭缺欠分類及說明》
17、GB/T13320-91《鋼質模鍛件金相組織評級圖及評定方法》
18、GB/T3098.1-2000/ISO 898-1:1999《緊固件機械性能螺栓、螺釘和螺柱》
19、GB/T 1172-1999《黑色金屬硬度及強度換算值》
20、GB/T11354-2005 《鋼鐵零件 滲氮層深度測定和金相組織檢驗》
21、GB/T 2654-2008/ISO 9015-1:2001 《焊接接頭硬度試驗方法》
22、ISO 5817:2003 《焊接-鋼、鎳、鈦及其合金的熔化焊接頭(高能束焊接頭除外)-缺欠質量分級》
23、BS EN 1043.1:1996 《Destructive tests on welds in metallic materials.Hardness testing》
24、GB/T 19869.1-2005/ISO 15614-1:2004《鋼、鎳及鎳合金的焊接工藝評定試驗》
25、JGJ81-2002 《建筑鋼結構焊接技術規程》
26、GB/T 10561-2005 /ISO 4967:1998 《鋼中非金屬夾雜物含量的測定標注評級圖顯微檢驗法》
27、DL/T 674-1999 《火電廠用20號鋼珠光體球化評級標準》
28、GB/T 9450-2005 《鋼件滲碳淬火硬化層深度的測定和校核》
29、GB/T 9451-2005 《鋼件薄表面總硬化層深度或有效硬化層深度的測定》
30、GB/T 6394-2002 《金屬平均晶粒度測定方法》
31、GB/T 231.1-2002/ISO 6506-1:1999 《金屬布氏硬度試驗 第1部分:試驗方法》
32、GB/T 17394-1998 《金屬里氏硬度試驗方法》
33、JB 4708 -2000 《鋼制壓力容器焊接工藝評定》
34、GB/T 4340.1-1999/ISO 6507-1:1999 《金屬維氏硬度試驗第1部分:試驗方法》
35、GB/T 224-87《鋼的脫碳層深度測定法》
36、GB/T 226-91 《鋼的低倍組織及缺陷酸蝕檢驗法》
37、GB/T6401-86 《鐵素體奧氏體型雙相不銹鋼中α相面積含量金相測定法》
38、GB/T 7216-87 《灰鑄鐵金相》
39、GB/T 9441-88 《球墨鑄鐵金相檢驗》
40、GB/T 13298-1991 《鋼的顯微組織檢驗方法》
41、GB/T 13299-1991《鋼的顯微組織評定方法》
42、GB/T 13302-91 《鋼中石墨碳顯維評定方法》
43、GB/T 13305-91 《奧氏體不銹鋼中α相面積含量金相檢驗測定法》
44、GB/T 1979-2001 《結構鋼低倍缺陷評級圖》
45、JB/T 5074-1991 《低、中碳鋼球化體評級》
46、YS/T448-2002《銅及銅合金鑄造缺陷和加工制品宏觀組織檢驗方法》
47、JB/T7710-2007《薄層滲碳或薄層碳氮共滲鋼件顯微組織檢驗》
48、GB/T11354-2005《鋼鐵零件 滲氮層深度測定和金相組織檢驗》
49、GB/T13305-2008《不銹鋼中a-相面積含量測定法》
50、GB/T13320-2008《鋼質模鍛件金相組織評定圖及評定方法》
51、GB/T 14979-1994《共晶碳化物不均勻度評定法》
52、GB/T 6462-2005《金屬和氧化物覆蓋層 厚度測量 顯微鏡法》
53、GB/T 10561-2005《鋼中非金屬夾雜物含量的測定 標準評級圖》
54、GB 5310-2008《高壓鍋爐用無縫鋼管》
55、GB/T 6417.1-2005《金屬熔化焊缺欠及說明》
56、YS/T 347-2004《銅及銅合金 平均晶粒度測定方法》
57、GB/T3246.1-2000《變形鋁及鋁合金制品顯微組織檢驗方法》
58、GB/T3246.2-2000《變形鋁及鋁合金制品低倍組織檢驗方法》
59、JB/T5108-91《鑄造黃銅金相》
1.常規金相檢測
1.常規金相檢測
焊接金相檢驗、鑄鐵金相檢驗、熱處理質量檢驗、各種金屬制品及原材料顯微組織檢驗及評定、鑄鐵、鑄鋼、有色金屬、原材低倍缺陷檢驗、金屬硬度(HV、HRC、HB、HL)測定、晶粒度評級、非金屬夾雜物含量測定、脫碳層/滲碳硬化層深度測定等。
2.現場復膜檢測
對鋼(鐵)水包、混鐵車、行車、各種壓力容器管道以及特種設備等的非破壞性的組織檢測,檢測結果精確,對所檢設備無任何破壞。
3、點腐蝕
點腐蝕概念:金屬材料接觸某些溶液,表面上產生點狀局部腐蝕, 蝕孔隨時間的延續不斷地加深,甚至穿孔,稱為點腐蝕 (點蝕),也稱孔蝕。通常點蝕的蝕孔很小,直徑比度小得多。蝕孔的最大深度與平均腐蝕深度的比值稱點蝕系數。此值越大,點蝕越嚴重。一般蝕孔常被腐產物覆蓋,不易發現,因此往往由于腐蝕穿孔,造成然性事故。
不銹鋼點腐蝕形成機理
不銹鋼點腐蝕形成機理
金屬浸入含有某些活化陰離子(特別是氯離子)的溶液中,只要腐蝕電位達到或超過點蝕電位(或稱擊穿電位),就能產生點蝕。這是由于鈍化膜在溶液中處于溶解以及可再度形成的動平衡狀態,而溶液中的活化陰離子(氯離子)會破壞這種平衡,導致金屬的局部表面形成微小蝕點,并發展為點蝕源。例如不銹鋼表面的硫化物夾雜的溶解,暴露出鋼的新鮮表面,就會形成點蝕源。
點蝕的發展是一個在閉塞區內的自催化過程。在有一定閉塞性的蝕孔內, 溶解的金屬離子濃度大大增加,為保持電荷平衡,氯離子不斷遷入蝕孔,導致氯離子富集。高濃度的金屬氯化物水解,產生氫離子,由此造成蝕孔內的強酸性環境,又會進一步加速蝕孔內金屬的溶解和溶液氯離子濃度的增高和酸化。蝕孔內壁處于活化狀態(構成腐蝕原電池的陽極),而蝕孔外的金屬表面仍呈鈍態(構成陰極),由此形成了小陽極/大陰極的活化-鈍化電池體系,使點蝕急速發展。
防止點腐蝕方法:
防止點腐蝕方法:
1)減少氯離子含量和氧含量;加入緩沖劑(如CNˉ、NO3ˉ、SO42-等);降低介質溫度等。
2)在不銹鋼中加入鉻、鎳、鉬、硅、銅等合金元素。
3)盡量不進行冷加工,以減少位錯露頭處發生點腐蝕的可能。
4)降低鋼中的含碳量。此外,添加氮也可提高耐點腐蝕性能。
判定不銹鋼的耐點腐蝕性能時常用“點蝕指數”PI來衡量,即
PI=ωCr+3.3ωmo+(13~16) ωN
一般希望PI>35~40.
Cr的有利作用在于形成穩定氧化膜。Mo的有利作用在于形成MoO42-離子,吸附于表面活性點而阻止Clˉ入侵;N的作用雖還無詳盡了解,但知可與Mo協同作用,富集于表面膜中,使表面膜不易破壞
相關標準
相關標準
ASTM G48-2009《用氯化鐵溶液測定不銹鋼和相關合金點腐蝕和縫隙腐蝕的試驗方法》
GB/T 17897-1999 《不銹鋼三氯化鐵點腐蝕試驗方法》
均勻腐蝕概念
在金屬與介質接觸的整個表面都發生的腐蝕類型。是全面腐蝕的一種形式。
機理
構成均勻腐蝕過程的腐蝕原電池是微觀腐蝕電池,而構成局部腐蝕過程的原電池是宏觀腐蝕電池。均勻腐蝕時,陽極溶解和陰極還原的共軛反應在金屬表面相同的位置發生,陽極和陰極沒有空間和時間的區別,因此,金屬在全面腐蝕時整個表面呈現一個均一的電極電位,即腐蝕電位。局部腐蝕由于金屬表面存在電化學不均勻性,陰極反應和陽極反應分別在陽極和陰極發生,陽極區和陰極區發生空間分離,陰陽極之間存在電勢差。
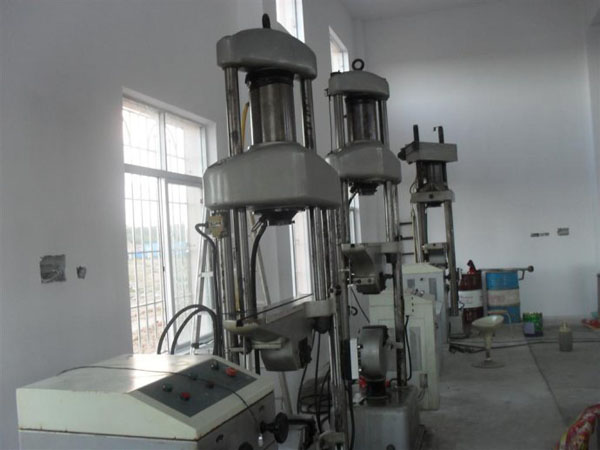
三.力學試驗
一、鋼結構力學性能檢測:
1. 金屬原材的拉伸(屈服強度、抗拉強度)、彎曲、沖擊、硬度等韌性和塑性性能檢測,鋼筋拉伸(屈服強度、抗拉強度)、彎曲等性能。
2. 金屬焊接件的焊接工藝評定。
二、鋼結構緊固件力學性能檢測
二、鋼結構緊固件力學性能檢測
螺栓連接副扭矩系數、緊固軸力、拉伸(屈服強度、抗拉強度)、硬度等性能、螺栓連接板抗滑移系數檢測。
金屬硬度試驗
是金屬抵抗局部變形,特別是塑性變形,壓痕或劃痕的能力,是衡量金屬材料軟硬程度的一種指標.
硬度試驗應用
靈敏反映材料在化學成分、金相組織、熱處理工藝、冷加工變形等差異;
試驗方法簡單,不必破壞工件,適合機械裝備和零部件材質現檢測;
試驗壓痕很小,可檢查金屬表面層情況,脫碳與增碳、表面淬火及化學處理后的表面硬度等。
應用特點
硬度值物理意義及其含義隨試驗方法而定
壓入法---材料表面抵抗另一物體壓入時所引起的塑性變形的能力;
刻劃法---抵抗表面局部破裂的能力;
回跳法---金屬彈性變形功的大??;
金屬表面上不大體積內抵抗塑性變形或破裂的能力;
“硬度”不是材料獨立的力學性能,其硬度值不是一個單純的物理量,是人為規定的在某一特定條件下的一種性能指標;
根據試驗原理方法的區別并根據被測試樣特性選擇合適的硬度試驗方法,從而保證試驗結果具有代表性、準確性及相互間可比性;
GB/T231.1-2002對原GB/T231-1984在下列技術內容進行了修改
取消了用鋼球壓頭進行試驗規定;
對布氏硬度計的要求完全按GB/T231.2執行;
將“試樣厚度至少應為壓痕深度的10倍”改為“試樣厚度至少為壓痕深度的8倍”;
取消了用直徑2㎜球壓頭進行試驗的規定;
鋼類的0.102F/D2僅用30的比率;
將“兩相鄰壓痕中心距離不應小于壓痕平均直徑的4倍”改為“兩相鄰壓痕中心距離至少為壓痕平均直徑的3倍”
增加了附錄C使用者對布氏硬度計的日常檢查方法。
標準只規定試驗力保持時間為10~15s,對于另取保載時間,只作保持時間允許誤差為±2s的規定。
布氏硬度試驗----
試驗原理
一定直徑的硬質合金球施加規定的試驗力壓入試樣表面,經規定的保持時間后,卸除試驗力,試樣表面就殘留壓痕,測量出壓痕直徑,求得壓痕球形表面積。布氏硬度值HB是試驗力除以壓痕球形表面積所得的商再乘以0.102。
試樣
試驗面應是光滑平面,表面粗糙度Ra一般不大于1.6μm;(原應在0.8μm以下)
在樣品的截取及加工過程中,應避免對試樣表面產生影響;
試樣支承面應平整并與試驗面保持平行;
試樣的厚度至少應為壓痕深度的8倍;(舊標準為10倍)
試樣的要點
試驗環境溫度|試驗儀器檢查|試驗臺、試樣放置及支撐|壓頭類型(材料)的選擇|壓頭直徑的選擇|試驗力的選擇|試驗力保持時間的確定|壓痕間間距;
布氏硬度應用特點
采用較大直徑球體,所得壓痕面積較大,其硬度值能反映金屬在較大范圍內各個組成相的平均性能,而不受個別微小不均勻性的影響。
壓痕較大另一優點是數據穏定,重復性強
適用范圍
鑄鐵﹑有色金屬及合金﹑特別對軟金屬,如鋁﹑鉛﹑錫等。
布氏硬度試驗缺點是對不同材料需要更換球體和改變載荷,壓痕直徑測量也比較麻煩。由于壓痕較大,不宜在成品上進行試驗。
洛氏硬度試驗----
洛氏硬度試驗----
試驗原理
洛氏硬度試驗原理與布氏方法不同,不是測量壓痕面積,而是測量壓痕深度,以壓痕深度的大小來表示材料硬度的。
試驗操作要點
試驗溫度|洛氏硬度標尺的選定|硬度計的檢查|試樣的支承與固定|試驗力保持時間|壓痕間距;
應用范圍及優缺點
通過變換試驗標尺可測量硬度較高的材料;
壓痕較小,可用于成品半成品檢驗;
操作簡便,工作效率高,適合于批量檢驗;
壓痕較小,代表性差;
不同標尺測得的硬度值彼此無內在聯系,也不能直接進行比較;
維氏硬度試驗----
試驗原理
維氏硬度的試驗與布氏硬度相同,也是根據壓痕單位面積所承受的試驗力來計算硬度值。所不同的是維氏硬度采用的壓頭是兩相對面間夾角為136°的金剛石正四棱錐體。
試驗操作要點
試驗溫度|試樣的固定|試驗力的選擇|試驗力保持時間|壓痕間距|壓痕的測量
應用范圍及優缺點
維氏硬度試驗主要適合測定各種表面處理后的滲碳層或鍍層的硬度以及較小、較簿工件的硬度,顯微硬度可測定組織中相硬度;
載荷從很小到很大,可任意選擇;
采用對角線長度計量,精確可靠;
硬度值測定較麻煩,工作效率較洛氏硬度低,所以不宜于成批生產的常規檢驗;
肖氏硬度試驗----
試驗原理
與上述各種靜態壓入法硬度不同,肖氏硬度是一種動態力試驗法;
采用具有一定重量和規定形狀的金剛石沖頭從一定高度自由落到試樣表面,根據沖頭回彈高度來衡量硬度值大小,因此也稱彈性回跳硬度;
試驗操作要點
試驗溫度|硬度計調整及檢查|試驗過程應保持平穩|操作應熟練|兩相鄰壓痕中心距離應≥1㎜,壓痕距邊緣的距離應≥4㎜;
應用范圍及優缺點
肖氏硬度試驗適合于在現場測試軋棍、機床床面、導軌、大型鍛件等工件硬度。操作簡便,測試效率高,試驗后工件上幾乎不產生壓痕,可用于成品檢驗。測試精度低,重復性差。試驗結果準確性受人為因素影響較大,不適合精度要求較高的試驗。對于彈性系數相差較大的材料,其所測硬度不能相互比較。
里氏硬度試驗---
試驗原理
試驗原理
用規定質量的沖擊體在彈力作用下以一定速度沖擊試樣表面,用沖頭在距試樣表面1㎜處回彈速度與沖擊速度的比值再乘以1000,定義為里氏硬度。
操作要點
操作要點
試樣試驗面符合要求|硬度計的檢查|試樣支承時,應保證其整體剛性|沖擊裝置支撐要求;
應用范圍及優缺點
應用范圍及優缺點
一般適合于大件的現場硬度測試;
操作簡單,測試效率高。
采用電子測量,數值顯示靈敏,測量精度優于肖氏硬度;
試驗時受試樣質量及厚度影響較大,一般不宜對薄板及薄管材進行檢測。
四.檢測設備
四.檢測設備